12.0 Biosecurity for Aquatic Livestock Production
12.3 Facilities
The foundation for successful production facility operations starts with the design stage. For example, space and traffic flows are considered and drawn into the facility plan. A site drawing is an excellent place to ask questions about how things will function. What do the neighbors do, and what activities might affect the fish rearing? How do feed trucks or harvest trucks approach the facility? Can truckers enter the production zone? What are the construction materials and methods? A future chapter will cover site location and facility design more elaborately.
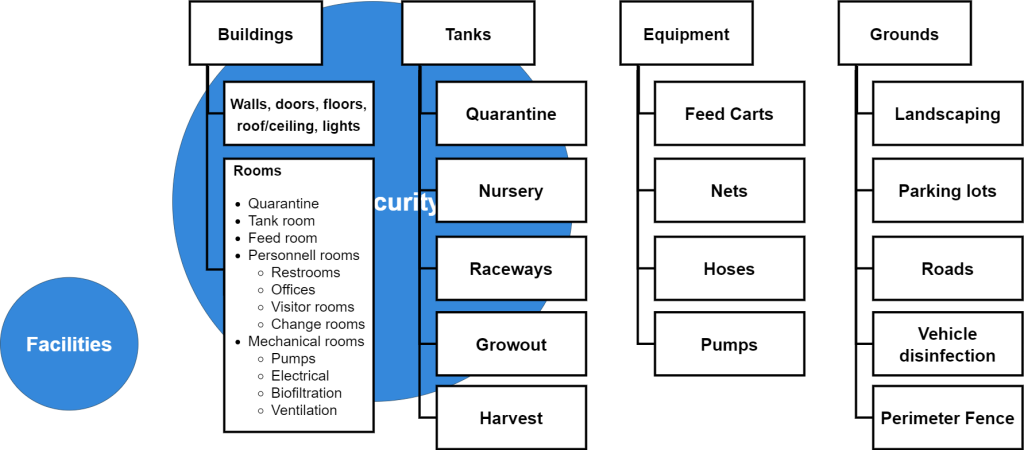
Facility construction and maintenance is a major support to the maintenance of the animal’s health, which, of course, is the central focus of operations. The critical space of the production facility can be pictured as a sphere or compartment with limited access and processes. The four subgroups displayed for facilities do not represent the complete list but are shown to illustrate some assets such as construction, equipment, and the location’s upkeep impacted by a BP.
Buildings
Buildings are enclosures with walls, doors, a roof/ceiling, and lighting. This enclosed space is divided into rooms for specific purposes or functions. Typical room functions are listed in the accompanying image. It is first necessary to identify production areas, where livestock are contained, versus support areas, which aid in production. The tank room is hopefully the core production area in the list of rooms. Feed rooms, power control rooms, the laboratory, and change rooms are support rooms. Some rooms will need direct access to the tank room, but others do not need to be directly connected to the core area of production.
Quarantine Areas
Quarantine areas must be completely separated in physical location and operations. Operational support includes mechanical rooms would include separate pumps, electrical, ventilation, and biofiltration spaces that are separately controlled from production operations. Production personnel must not maintain or operate support areas without proper disengagement followed by support role preparation. This requirement does not prevent safe evacuation routes, but the human movement from production to support areas or the outside must be controlled. Production personnel spaces include separate restrooms, change rooms, lunchrooms, and specific offices. Administrative and support employees should be separated from production employees by use of different traffic flows and assigned spaces to prevent contamination. Management does not have justification to enter production areas unless it is worth following production employee entry protocols. Most importantly, interpersonal communication can be done via windows or electronics. Successfully isolated facilities utilize visitor mezzanines and observation windows to inform the public or potential investors of the layout and operations.
Tanks
Tanks that are properly designed and of impervious, cleanable construction will be needed. Proper design allows for sufficient water exchange to maintain lower stress and better livestock health. Exceptional tank designs include the ability to isolate tanks from the system as a whole to limit disease spread, allow treatment, and permit complete cleaning and disinfection after depopulations.Circular tanks can have several advantages, including providing a uniform culture environment and can prevent and remove settleable solids. However, circular tanks are only one of many designs that have been used successfully over time. Tanks constructed of metals such as stainless steel are not competitive. Concrete tanks may be suitable in cost but generally require surface coating(s) to prevent corrosion and assure cleanable and impervious surfaces. Production tanks may be divided into segregated groups that separate life stages. Segregated use of tanks also assures proper water flow and routing to keep different production populations separated from each other and in an optimal production environment.
Equipment Lists
The equipment list (Image 12.04) includes carts, shovels, hoses, nets, and other mobile items. The biggest caution is about the mobile equipment and the procedures necessary to make certain equipment is sanitized and used in designated areas. For example, each tank must have its net(s) and a designated sanitizing station. The argument of all tanks being interconnected by water flow in a common system does not hold much value when the water is recycled through water treatment systems with sand filters, UV lights, and even ozone administration. Therefore, nets can spread disease from tank to tank when not controlled. (See Processes for handling net handles with gloved—not bare—hands.)
Cleaning
Floor cleaning with water spray could cause aerosolized pathogens from the floor that could settle into production tanks. Floor cleaning procedures must be done often and gently. Pooled water on floors is also contrary to biosecurity because the floors are constantly wet in those areas. Standing water is often a source of microbial contamination, only worsened by hose spraying. Hoses are also a biosecurity risk when not properly cleaned and sanitized before proper storage. Additionally, hoses trailing through the production area can interfere with floor cleaning.
Facility Design
A new facility designed for a specific purpose will have the opportunity to avoid many of the pitfalls of a refurbished facility. Remodeling a swine barn to hold fish tanks may seem simple, but problems arise from drainage, traffic patterns, ventilation, environmental controls, and many other parts of the operations.
Facility layouts in new construction can optimize traffic flows, feed routes, and other daily procedures. New construction has choices of location to eliminate the risks to production that established facilities do not have concerning activities of neighboring properties or wildlife harborages. This comparison of new versus remodeled facilities is a serious one to have in planning the siting of a new or repurposed production site.
Significant design quality of a production facility provides permanent surfaces that are impervious and cleanable. The higher the grade of surfaces, the less impact microbes generally have because they are more readily removed with cleaning. Sufficient cleaning is required before disinfection of surfaces can be considered. Many disinfectants can be hindered by organics covering the surface. Bleach, for example, cannot remove the so-called biofilm impervious to chlorines. Other disinfectant options include physical methods such as heat, sunlight, and drying and chemical disinfectant methods such as Virkon Aquatic, chlorhexidine, quaternary ammonium compounds, and alcohols. Clean surfaces can be disinfected and permit other biosecurity efforts to be effective. Easy to clean surfaces should also be incorporated into the design of production facilities. Rather than having a 90-degree corner, the design at the surface corners of tanks can be curved, allowing brushes to easily scrub the surface and clean more efficiently. Coving at the junction of the floor and wall should be rounded and tightly sealed to those surfaces to allow better scrubbing and disinfection.
Facility Grounds
The facility grounds are those areas surrounding the facility. These can be functional and decorative. Hard-surface walking and vehicle drives are functional, while landscaping shrubs are decorative. The perimeter fence or other physical barrier is often functional and decorative. The level of functionality is defined to assure that it is effective. Will the property border fencing mark out the perimeter? Will the perimeter barrier effectively prevent larger rodents and other vermin from migrating into the facility grounds? Hard-surface drives for vehicles are even more functional when vehicle wheel disinfection is designed into the structure of the roadway. Facilities can build a wheel wash basin to remove debris and materials that could be carried in from other facilities or have crossed paths with infected traffic. Installation of these basins takes design efforts to prevent freezing in cold climates. The basin must not be allowed to accumulate debris or become low on disinfectant concentrations. Birds can also be fomites of disease; therefore, buildings should be designed so as not to leave roosting structures available to wild birds.
Feed spills must be cleaned immediately to reduce the attraction to birds and rodents, which come to the facility for feed and harborage (safety). If rats are a problem, the building can be landscaped with a zone of larger pebbles extending at ground level from the foundation that deter the animals from burrowing under the building. Extraneous and excess equipment must not be stored next to the building. Smaller equipment can be located on pallets elevated by over 12 inches to prevent most rodents from claiming the generated structure of stored equipment as a harborage. Building entrances (i.e., doors) must be weather tight, vermin proof, and closed when not in use. Doors must be immediately closed as rodents will migrate indoors any time there is less threat of discovery. Doorways are not installed for ventilation, and vents can be installed in doors that permit airflow and prevent access points to vermin. Even worn weather stripping on the bottom of truck entrance doors can give access to mice seeking entrance into feed storage areas.
On the farm, keeping dry feed in vermin-proof compartments is paramount. Grain silos with chain feeders to each tank are recommended as long as the feed cannot get held up and become moldy. Inspection and remediation are important even if the machinery is “automated.” Otherwise, bagged feed can be used and needs to be on pallets rather than stacked against the walls. The distance from the wall permits inspection for indications of rodent infestation. Ideally, feed is kept 12 inches off the floor or moved every 7 days. Not least is the effort to keep vermin outside the feed storage room with closed, tight-fitting doors and screened windows. When facilities are designed, constructed, and maintained in compliance with the BP, they resemble the illustrated visualization Image 12.05.
Evaluating Facilities
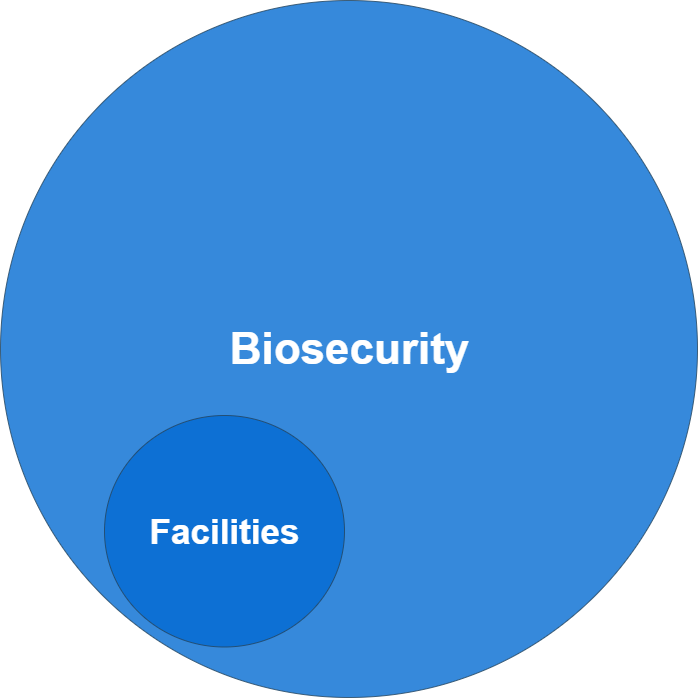
Veterinary evaluation of facilities and operations may be performed best with the same areas in this “four circles” paradigm. In production animal medicine, the four circles consist of the exterior of the building and surroundings, interior and housekeeping, animal enclosure size and density, and individual animal. Each step considers how that aspect may affect the health of the livestock. In aquaculture, the exterior of the building, interior of the building, and tank are similarly important to the health of these animals. Walking the perimeter of the building during biosecurity audits allows evaluation of outside activities, vermin control, and vehicle and personnel traffic patterns to provide better animal health planning and increase animal welfare.
Facility design/construction and management of the facility are typically not interchangeable. If the feed room door on a refurbished building never had a weather seal, the management option would be to install the weather seal. Yet effective management is about maintaining the facility, not redesigning or rebuilding it. Remodeling facilities often leaves management in a bind for time or materials. These obligations to upgrade a facility are the proverbial “death by a thousand pinpricks,” creating an operational expense rather than a capital cost in the start-up financing area. If a design is not professionally evaluated before construction or remodeling, risk to the business profitability can exceed the profit potential.
The reader may have noticed the potential overlap between biosecurity auditing and engineering review. There are seemingly common aspects. The biosecurity audit has animal health (production efficiency and profitability) as the focused outcome. The engineering review focuses on facility maintenance and life span (reducing overhead and capital expenses). One professional must not feel encroached upon by the other when both work in the same facility. Both are useful and complemental to the operations. This author has benefitted enormously from studying engineer reports when available and hopes the reverse has been true for the engineer(s).